Laser Cutting for Prototyping: Speed, Precision, and Cost Savings in Electric Motors
Laser cutting for prototyping ensures precision and speed, reducing costs and optimizing electric motor production with complex geometries. 15-03-2025
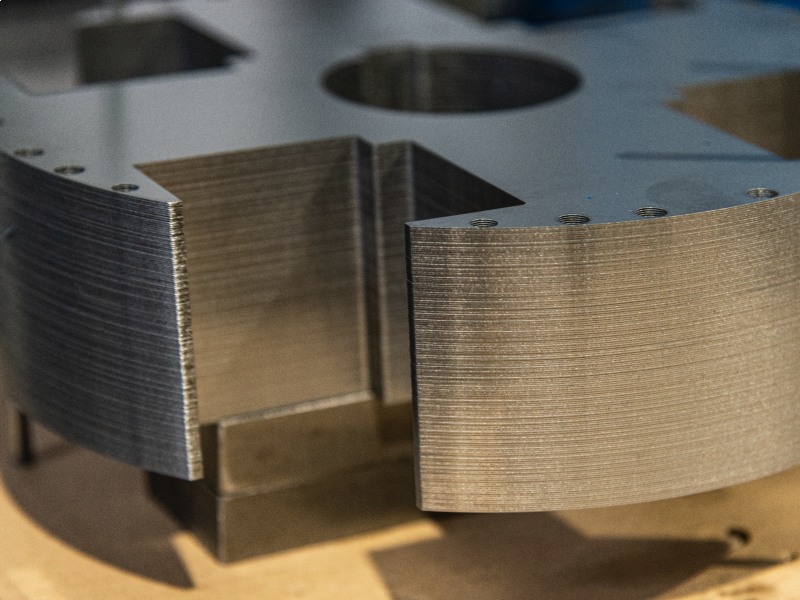
Prototyping is a critical phase in electric motor production, where every detail is tested and refined before moving to large-scale manufacturing. Among the most advanced technologies used in this stage, laser cutting stands out for its speed, precision, and cost efficiency, offering a flexible and effective solution. This technology allows for highly accurate prototypes, optimizing both time and resources without compromising quality.
What is Laser Cutting and What are the Benefits?
Laser cutting is a manufacturing process that uses a high-power laser beam to engrave and cut materials with extreme precision. This technique is particularly suitable for magnetic laminations used in stators and rotors of electric motors, enabling the production of complex and detailed geometries without the need for mechanical tools.
Key Benefits of Laser Cutting:
- Fast execution: Prototypes can be produced in shorter timeframes, accelerating development cycles.
- High precision: Laser technology ensures minimal tolerances, producing components that perfectly match the design specifications.
- Flexibility: Design modifications can be implemented instantly, without additional costs for tools or molds.
- Lower initial costs: The absence of toolings significantly reduces startup costs, making this technology ideal for prototyping and small series production.
Laser Cutting in Electric Motor Prototyping
In electric motor manufacturing, prototyping must meet specific performance, efficiency, and durability requirements. Laser cutting enables the testing of new design solutions with maximum fidelity to the original concept, providing a rapid method to verify component functionality before full-scale production.
Thanks to its high precision, laser cutting allows for magnetic laminations with extremely tight geometric tolerances, enhancing motor efficiency and reducing energy losses.
Combining Laser Cutting with Other Technologies: Punching and Progressive Tools
Laser cutting is often combined with other manufacturing processes to further optimize production. Specifically, for large electric motors or high-volume manufacturing, laser cutting can be combined with notching, which reduces large production costs even further.
When transitioning to mass production, progressive die stamping enhances productivity and lowers long-term costs. However, in the early stages of development and testing, laser cutting remains the most efficient and flexible solution.
Laser cutting is a key technology for electric motor prototyping, providing speed, precision, and cost reduction. Its flexibility allows for testing new geometries and materials without manufacturing constraints, accelerating the development of innovative solutions.
Investing in advanced prototyping technologies means obtaining high-performance, reliable components, shortening time-to-market, and enhancing final product quality. For companies in the electric motor industry, laser cutting is a winning choice to tackle innovation challenges with efficiency and competitiveness.